The main advantage of magnets produced by injection moulding is the more or less free design of the part geometry. This is inserted mechanically into a corresponding injection mould as a negative mould once or several times in order to produce one or more parts per injection cycle. Magnets with or without inserts can be produced in one step. Depending on the selected material, these can be magnetised either during the injection process in the mould or in a downstream, separate process step. Injected magnets usually do not achieve the magnetic values that e.g. pressed or sintered magnets do. One of the reasons for this is that the degree of filling, as a ratio of magnetic powder to binder (thermoplastic), must be significantly lower than with the pressed magnets. This is to enable the respective materials to be injected as a homogeneous melt into the mould until it is completely filled and only then solidify.
Injection-moulded magnets are used in a wide range of technical applications. For example, they are used as signal transmitters for position or motion scanning, as magnetic couplings or as rotors for small-sized electric motors.
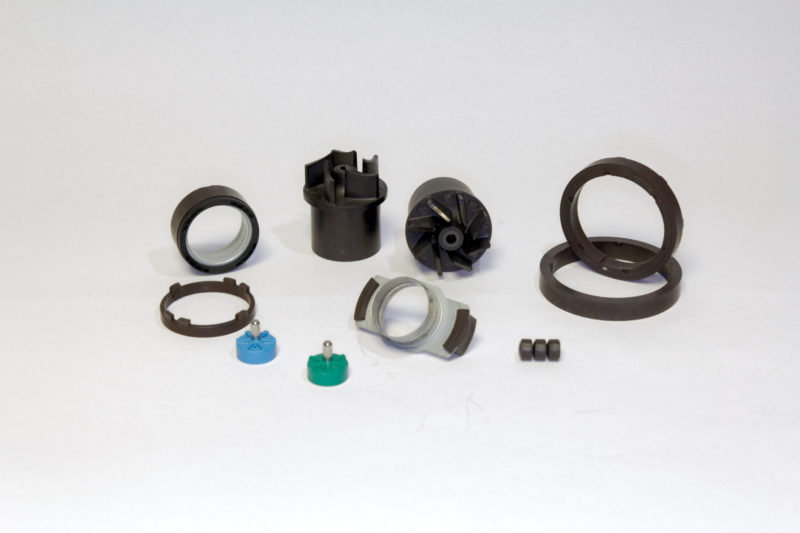