Der Hauptvorteil von Magneten die im Spritzgießprozess hergestellt werden ist die mehr oder weniger freie Gestaltung der Artikelgeometrie. Diese wird durch mechanische Bearbeitung einfach oder mehrfach in ein entsprechendes Spritzgießwerkzeug als Negativform eingebracht, um je Spritzzyklus ein oder mehrere Teile herzustellen. Es können Magnete mit oder ohne Einlegeteil in einem Arbeitsschritt hergestellt werden. Diese können, je nach Materialauswahl, entweder bereits während des Spritzprozesses im Werkzeug, oder in einem nachgelagerten, separaten Prozessschritt magnetisiert werden. Gespritzte Magnete erreichen in der Regel nicht die magnetischen Werte wie z.B. gepresste oder gesinterte Magnete. Dies liegt unter Anderem daran, dass der Füllgrad, als Verhältnis von Magnetpulver zum Binder (Thermoplast) deutlich geringer gewählt werden muss als bei den gepressten Magneten, damit die jeweiligen Werkstoffe solange als homogene Schmelze in die Form gespritzt werden können bis diese vollständig gefüllt ist und erst dann erstarren.
Gespritzte Magnete kommen in weiten Bereichen der Technik zur Anwendung. Zum Beispiel als Signalgeber für Positions- oder Bewegungsabfragen, als Magnetkupplung oder als Rotoren für kleinere Elektromotoren.
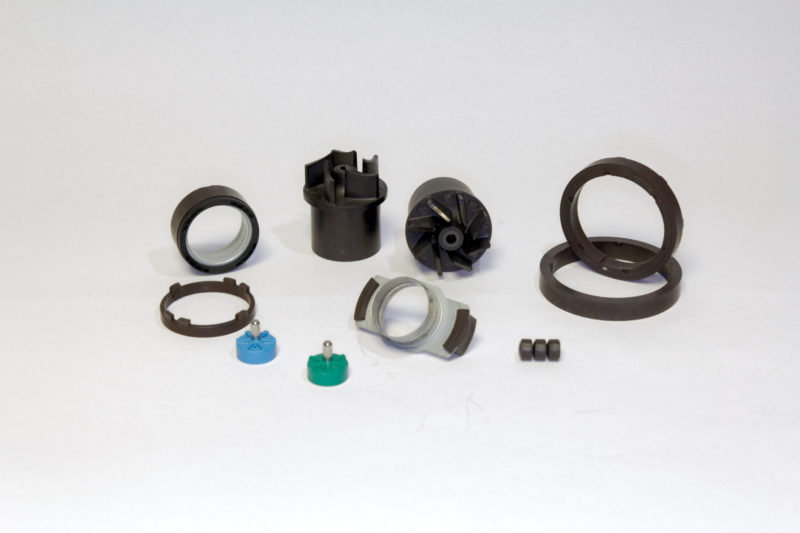